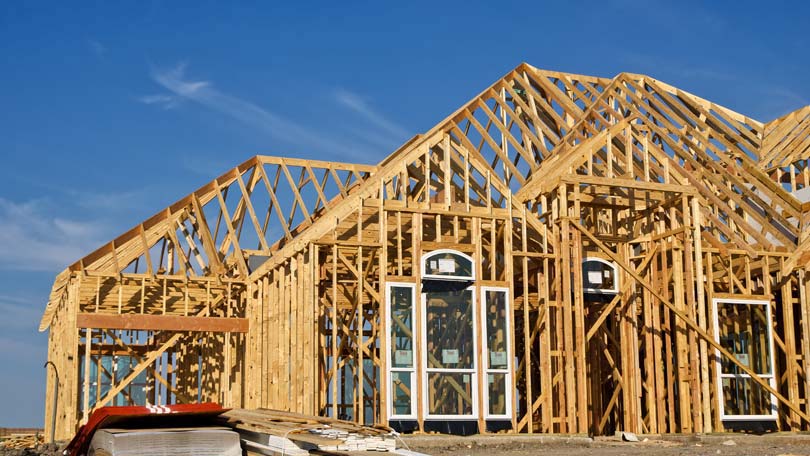
Professional builders and quantity surveyors know how important it is to have accurate estimates and costings when doing any form of construction. They also know how important it is to set a realistic budget and then stick to it. If you have owner-built a house, you probably realize this as well.
There is no doubt that the best way to squander money when building your own home is not to cost the project accurately in advance. Another is to try and build something that you can’t afford. Since a wide variety of circumstances can affect costs during the building process, it is also vital to control the impact of changes to original cost estimates.
Sometimes people talk about costs of building per square meter. But the variations of choice are so vast this is an impossibly simplified idea. In a word: useless. A more reliable method is to base estimates on a percentage of what each aspect of the building process should cost. But even this is potentially flawed because it depends on so many variable factors from the building site and construction methods used, to the wide range of fixtures, fittings and finishes chosen.
So how do you work out a reliable cost breakdown of building a house?
Establish what you want and what you can afford
The choice of building types is remarkably vast and varied, ranging from timber-frame to rough stone construction, and from cottage to castle. A wide variety of building techniques have been developed over the centuries, many of which vary from country to country, depending on climate, natural resources, socio-economic needs, available products, and also trends and fashions. Happily there is an increasing choice of eco-friendly products that we can use.
First you need to know what it is you are going to build (or want to build), in terms of size and style. Then you need to know what basic materials you are going to work with, timber or bricks and mortar being the two most obvious generalizations. But even within these two building methods, there is enormous choice in terms of both material and method. For example, brick walls may be solid, or they might be built with a cavity between two brick skins. The outside of the walls might be built using facing bricks or they may be built common building bricks and then rendered with a plaster mix and painted. Alternatively they may be stuccoed using a finish that does not have to be painted.
Timber homes often have a brick or simulated stone exterior or veneer. This is really no more than a cladding material although the veneer wall must be constructed on the foundation of the house. Walls of timber homes may otherwise be built with a timber exterior, or with some other type of cladding.
The building method you choose will also determine the type of foundations and footings you will need to construct.
Once you have a good idea of what you want to build, you need to get very specific and compile:
a) a detailed schedule of finishes, which must include all the exterior and interior materials and finishes you need, and
b) a detailed bill of quantities that how much or how many of each item on the schedule of finishes you need.
Only then can you accurately establish what the house is going to cost to build.
Of course, if you are employing an architect or similarly trained technologist to draw plans for you, you will need to ensure that he or she knows the type and style of house you prefer as well as desired building method you want to use. You should discuss your needs in terms of specific material choices and the fixtures, fittings and finishes required, as well as your budget constraints before even sketch plans are prepared.
Schedule of finishes
Specifying materials and compiling a good schedule of finishes can be difficult if you don’t have any real knowledge of the building industry. In this instance it makes sense to seek professional help. However if you know what you want, and enjoy shopping around, then there’s no reason why you shouldn’t be able to compile your own schedules.
Ideally you should have your house plans before you make a final decision on your materials and finishes. However if you are inexperienced, but determined to do your own cost breakdowns, then it is best to use a sample floor plan that is similar to what you have in mind. These are reasonably easily sourced from home plan web sites.
Today there are many computer-generated software packages that you can use to do specify as well as quantify and cost building projects (see below, Software that produces the cost breakdown of building a house). These usually include guidelines and lists in generic categories, for example:
- Preliminary and general (which would include permits, plant and so on as well as water and sewer tap-in fees) which will account for an initial 1.5% or more of your budget, depending on what is required, plus 4% for the tap-in fees,
- Utilities (electricity, gas, telephone and so on, if not included in general) which will take up at least 1% of your budget, largely depending where exactly you are located,
- Earthworks and excavation which will take up approximately 2% of your budget, more if it is a steep, difficult site,
- Concrete work (which would include foundations and footings as well as other concrete slabs or flatwork) which usually accounts for as much as 9% of budget,
- Brickwork (even if the house is timber frame, foundation walls might be built with bricks or blocks and there might be a brick or prefabricated concrete fireplace) and/or siding will take at least 7% of your budget. If built using bricks it could be as high as 14%,
- Door and window frames plus doors and windows, which will total about 5% depending on your choice,
- Timber and trusses (for a timber frame house these categories might be separated); at least 10% to get the house to the dry-in stage of building, where the shell is complete and waterproof, plus labor that will also account for about 10% of the budget,
- Dry walling, which presuming this is the building method used throughout the house will account for about 5% including labor and materials,
- Roof covering, which will account for at least 5% of your budget and as much as 11% if expensive shingles or tiles are chosen,
- Plaster and screeds, no more than 2% if the house is timber frame, but if it is built with bricks, as much as 8%,
- Ceilings, about 3%,
- Glazing, no more than 1%, unless of course the design of the house incorporates lots of glass or triple glazing is used throughout,
- Carpentry and ironmongery (including timber doors, skirting, and door hardware) around 4%,
- Tiling and floor covering (which would include both wall and floor tiles), around 6% depending on quality,
- Plumbing (from gutters to geysers and of course all the sanitary ware and sinks for bathrooms and kitchens) will take about 6% of your budget,
- Electrical and gas (including light fixtures), 5%, 1% of which accounts for the fixtures and fittings,
- Heating and insulation, both of which are essential in North America and other cold-winter countries, 5.5%,
- Paintwork, 4% for a professional job, including labor,
- Appliances (some of which you may already have) shouldn’t take up more than 2% of budget,
- External site work (which would include any patios and paving, and possibly landscaping of the garden), about 4%,
- Other provisional amounts (for example built-in cupboards or decks), about 67% including interior trim and the labor to undertake the work.
While this is a pretty simple list, within each category come numerous sub-categories. If you are likely to spend more than the percentage shown in our list, you will need to adjust another category’s allocated percentage otherwise you will be over budget before you even begin.
More detailed considerations within the cost breakdown of building a house
It is vital to be aware of the vast variations of quality and cost in the building industry.
Doors & Windows
For example if you consider door and window frames, these may be wooden or metal (some of which are hollow) and produced in a wide variety of sizes and styles – and of course prices. Some are hinged and some slide, including the ingenious Kristrack Multi Sliding System for Doors and Windows (www.kristrack.com). The company, which has a manufacturing plant in Burnaby, Canada also supplies pocket door hardware systems which a great when saving space is an issue. Even though they are more expensive than the average hinged frame, your ability to use them to save space will in itself save money.
When it comes to doors, there are so many possibilities it is mind boggling. Just go to Lowes to get some idea of the range of styles and materials used for exterior doors. The Lowes has doors made from wood, steel, aluminum, fiberglass and even vinyl, again in a wide range of prices. They’ve got double doors and single doors, solid doors and doors with glass panels – all suitable for a front door. They also stock a wide selection of patio doors which may also be hinged or sliding and made from the same materials as their front doors, as well as some that are clad with wood. While you may prefer to try and minimize costs by buying doors and windows directly from a manufacturer, this type of outlet is great for getting a really good idea of what is available on the market. Also, not all manufacturers will sell direct, so you might have to buy from a building store like this one.
Then there’s the issue of saving energy. By choosing energy efficient door and window products, you can quickly cut down on your energy bills (even if it means you have to spend a little more on good quality, well insulated windows that incorporated recycled materials) – and you can ease your conscious knowing that you have done your bit to help reduce greenhouse gas emissions.
All Weather Windows (www.allweatherwindows.com) is a North American company that has a positive and very effective recycling program and conservation initiative. For example they recycle more than 2,000 lbs of PVC at their Edmonton factory every single day. They are also recovering 100% of the PVC waste that is created during the manufacture of PVC door and window products. Cut-outs from all polyurethane insulated door panels are also recycled, and so is the cardboard used in production of cellulose fiber insulation.
Cascadia – www.cascadiawindows.com– specializes in fiberglass doors and windows that are fitted with high performance glazing. These are highly energy efficient, so you can be sure that your energy bills will be minimized even if you spend a little more than your allocated budget.
Flooring:
Flooring is an area where there is loads of choice from tiles or carpet fitted on a concrete slab to suspended timber floors. It is also an area where there are some exciting “green” options that are not only sustainable but incredibly good looking as well. Instead of cutting down trees to make wooden flooring, a growing number of manufacturers have turned to materials like bamboo and sustainable palm trees. Many of those who still produce solid wood products make sure that they source their lumber from sustainable forests where trees are grown specifically for the building and related industries.
Smith & Fong Co – www.plyboo.com – was the first North American company to import bamboo plywood and flooring. Bamboo is, of course, one of the most rapidly renewable materials available. Today the company offers more than 25 SKUs (stock taking units) with a variety of grains, and more than 50 SKUs of bamboo plywood products. The visual effects are immensely different and quite unlike conventional flooring products, many of which are not made from sustainable materials. Like their bamboo flooring products, Smith & Fong Co’s palm flooring is recognized as “leading-edge” in the green building industry and is rapidly gaining popularity in the home building market.
Shaw Floors – www.shawfloors.com – also focuses on “green” products, for example top quality carpeting that will reduce your energy bills because they provide natural insulation that is up to 17 times more effective than other flooring. So even if their carpets are more expensive than another company’s, you can adjust your percentages in the bill of costs by reducing the insulation budget and slightly increasing the budget for flooring. This same company also offers environmentally friendly tile and stone products, including some that contain as much as 40% recycled materials. And they produce eco-friendly hardwood products including one that uses less harvested wood and incorporates an inner layer made from recycled wood fiber.
Roofing:
Roof covering is yet another category where there is loads of choice, but it is essential to remember that whatever you choose will determine the structure of the roof itself. For example, roof trusses are spaced a lot further apart for sheeting of all kinds than they are for tiles, relatively lightweight coated metal pressed tiles being the exception. So even before you consider the actual cost of the roof covering you should take the cost of your trusses into account. Having said that, the cost of trusses must be seen in conjunction with the cost of whatever roof covering you decide to use. If you are using tiles or shingles, a good rule of thumb is that lighter material is usually cheaper, needs less support (which is where your roof trusses and purlins or battens come in), and is cheaper to lay than heavier tiles or shingles. The steeper the pitch of the roof is, the more expensive the tiles or shingles will be. But this factor can even out. For example, concrete tiles must be laid at a fairly steep pitch (26° compared to a minimal 5° pitch for sheeting), which means labor costs will be a little higher than they will for sheeting. But they are considerably cheaper than other tiles. In fact Unicrete roofing tiles are said to last as long as cedar shingles, which we all know keep going for generations.
Whichever material you are choosing and costing, have a look at all the possible options. We are all gravitating towards houses that are more sustainable than in the past, and there are some fascinating options that may be considered. One that is grabbing people’s attention right now is shingles made from recycled rubber tires. They look much the same as slate and cedar slates and shingles, but they have a whole lot of other advantages, not least of which is that they aren’t damaged by hail or by major extremes of temperature. They are also maintenance free and so far have stood the test of both wind and time, however short. Several companies make these shingles, including the US Minnesota-based Hi Tek Rubber Inc., and Canadian-based Euroshield (www.euroshieldroofing.com) which has been manufacturing rubber roofing systems for more than a decade.
Lumber:
The allocated budget for timber and trusses is relatively high (10%) and it really does pay to use quality lumber. An amazing energy efficient and environmentally friendly product that has been developed for conditions in Canada comes in the form of new age BluWood – www.bluwoodcanada.com. A trademarke, two-part wood treatment product that is applied in the factory, it comes with a lifetime warranty and provides protection against mould, fungus and insects (including termites) for all timber components in the structure above the ground.
In all instances labor will have to be factored into the calculations. Sometimes items are supplied and fitted by the supplier – glazing and aluminum window and door frames for example. In other instances, specialist contractors or skilled laborers will be required. Generally it is best to avoid paying sub-contractors by the hour or by the day because it precludes you from making an accurate costing in the planning phases. If you are employing laborers and overseeing work yourself, you may be forced to pay according to time worked.
Paint:
Painting is one job that often attracts an hourly or daily rate – that is if you don’t employ a sub-contractor who charges for the job. Whether you are doing the job yourself or hiring an outsider, make sure that the best quality paint is used, and preferably one that is “green” or environmentally friendly. Benjamin Moore (www.benjaminmoore.com) and General Paint (www.generalpaint.com) are both quality brands that Canadians know and appreciate. While Benjamin Moore has a relatively new eco-friendly zero-VOC paint product, Green Paint specializes in health, eco-friendly paints for homes. The company also supplies bamboo flooring. Compare products and prices before you make a final choice.
Where specialist companies are to be used – for instance to design and fit the kitchen or to do all the landscaping – obtain firm quotations before finalizing contracts. These figures would usually be inclusive and simply added to your own costing estimates. In any case have a look at what reliable, well known companies produce, like Huntwood (www.huntwood.com), which produces eco-friendly solid wood kitchen cabinets, or Kingwood Cabinets (www.kingwoodcabinets.com), which only uses wood from sustainable forests.
Once you have your schedule of finishes, and detailed information about all items in it, you can use it to prepare a reasonably reliable costing estimate for the house.
Quantifying and costing building projects
There are many different ways to owner-build a house. Some people love the challenge of a hands-on approach where they get involved and do the work – or some of it – themselves. Others prefer to employ others and supervise the construction process. Many owner-builders opt to employ a project manager to handle the day-to-day site work, but still keep a hand in the project to check both quality of workmanship and cost control.
It is no secret that efficient cost control is one of the biggest issues people have when they build houses or even when they have them built by building companies. It is absolutely vital to know what quantities are required, how much these will cost, and where money has been spent at any one stage.
One thing you must always remember is that a lack of cash flow can quickly create problems with a building project (particularly a private home that is being built by the owner). If you don’t have the cash to continue building – be it your own or money supplied from a bank or another lender – you might put the entire project at risk. A horrifying number of home builders have found they have been unable to complete their homes because of cash flow problems. What this means is you absolutely must monitor what you are paying for materials and construction and compare these figures regularly with the figures in your budget. This is basically the cost breakdown of building a house that you should have prepared.
A competent and accurate running estimate will not only help you keep on track, it will also be information that you can (and will probably be required to) supply to your lender, if you have one.
There are many different ways to cost projects, but what is undeniable is that the more detailed it is, the more accurate it is likely to be.
The idea of relying on a cost per square feet is not accurate. The easiest way to illustrate this is to shows two houses that have a common area of say 400 square feet and to compare two different configurations. A square building will have four exterior walls that are 20 feet long, so the walls will total 80 feet in length. A longer rectangular building (10 feet x 40 feet and so also 400 square feet in size) will have longer walls in total – specifically 100 feet in all. Also it isn’t just floor area that determines what building is going to cost, as you have seen.
When quantifying and costing, it is important to be methodical. Approach the costings in a logical order, similar to that shown in this list above. Get quotations and bids for materials and any parts of the project you are going to sub-contract out. Shop around for the best prices but don’t choose the lowest price unless you are sure quality is acceptable and comparable.
Once you have prepared a detailed summary of costs, with subtotals for each section of work to be completed, you will find that it is reasonably easy to keep track of whether you are on budget or whether you are overspending.
While there is nothing to stop you keeping track manually – simply by writing everything down and noting expenditure, computer software simplifies this task and is considerably more accurate than most people’s maths!
Software that produces the cost breakdown of building a house
Long ago, before the age of computers, quantity surveyors had an enormous amount of paperwork to do to ensure accurate bills of quantities and cost estimates. Today there is a profusion of excellent software that they can use for every possible type of building project. Many packages are simple enough for owner builders to use. Even if you plan to employ a building company to construct your home, you might like to do your own cost breakdown to see what you are going to have to spend to get your dream home.
If you have never used any type of accounting or costing software, it is probably a good idea to experiment with free software first. If you take a bit of time to search the Internet you will probably be amazed at just what is available.
Here are just a handful of examples:
American home builder and author Carl Heldmann (whose book Be Your Own House Contractor was first published three decades ago) offers a free cost estimate spreadsheet package on his web site www.byoh.com. He has categorized the entire building process, starting with permits, fees and surveys, and specifies a recommended percentage of the entire project that should be spent on each category. It is similar but not the same as the percentages we have recommended.
Another great free product is the on-line calculator at www.building-cost.net. This tool will enable you to cost your building within 34 construction categories. It does, however, work on fairly broad “quality classes” of materials, and a per square meter cost, which is not very reliable. However it is based on a very reputable publication, the National Building Cost Manual which is produced annually by Craftsman Book Company. The 2011 edition (the 35th published by this company) costs $39.75 to download and $53.00 for the download plus the hardcopy version and a CD. It calculates cost estimates based on job sites in the United States.
Then there’s free bill of quantities software called PriMus-DCF which was developed by ACCA, an Italian software company that specializes in the building industry. Even though it has the Euro as its default currency, you can change this. You will however have to input all the prices yourself – which in the long run should make your estimates totally reliable.
Of course there are numerous cost estimating software packages that you can buy. Shop around and see if there are free trial options for those that appeal to you. That way you can make sure that this really is the best option to enable you to get a realistic and accurate cost breakdown of building a house before you spend money on the software.